
3D printed brain model for surgical simulation by Stratasys Direct Manufacturing.
It was only a year ago that some in the prosthetics field feared that advances in 3D printing technology might put them out of work.
“The feeling was that 3D printing would take away people’s jobs,” said Jeff Huber, cofounder of San Francisco-based Standard Cyborg.
The healthcare field is one area where 3D printing is poised to make a big impact, contrary to any fears prosthetists or other medical practitioners have about new technology infiltrating a traditionally staid industry. According to research firm IndustryArc, the global market for 3D printing in healthcare is expected to be worth $1.2 billion by 2020.
Additive manufacturing, commonly referred to as 3D printing, is the process by which objects digitally created in software are physically printed out in three dimensions as layers of melted plastic or powdered metal are stacked one upon the other. It’s a technology that has been around since the 1980s. but the development and promulgation of cheaper 3D printers that range in price from $2,000 to $8,000 and can fit on a desktop that began this decade
It’s a technology that has been around since the 1980s. However, the development and promulgation of cheaper 3D printers that range in price from $2,000 to $8,000 and can fit on a desktop that began this decade mean that 3D printing technology is becoming available to more people spread across numerous industries, including healthcare.
In 2016, 3D printing’s push into healthcare continued.
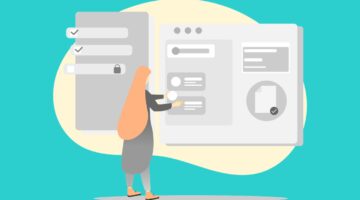
Solving Healthcare’s Provider Data Problem Starts with Interoperability
Break down the silos. Take control of your provider data.
In March, Spritam, the first 3D-printed prescription drug that received Food and Drug Administration approval in 2015, became available in the U.S. for treating seizures. Medical devices made from 3D printing now include instruments used for surgery or devices implanted into patients, such as the FDA-cleared, titanium-made bone tether plate produced by the Atlanta-based company MedShape.
And institutions such as Boston Children’s Hospital are increasingly turning to 3D-printed models of organs and bones to plan and practice complex surgical procedures. Earlier this year, the St. Louis University Department of Neurological Surgery partnered with the St. Louis School of Engineering to design lifelike 3D-printed models of brain aneurysms. Stratasys Direct Manufacturing, the in-house service arm of Stratasys, one of the world’s largest manufacturers of desktop and industrial 3D printers, printed the final models.
Every aneurysm is different in size, contour, and location.
“We have hundreds of clip sizes and types we can use [to close the aneurysm area] and we’re typically making the decision on clip size during surgery,” said Dr. Saleem Abdulrauf, the neurosurgeon-in-chief at the St. Louis University Hospital, who performed a simulated aneurysm surgery on the 3D-printed model. “If I can make that decision beforehand by practicing on a model, … it really makes a difference during surgery.”
Analysts have predicted that 3D printing will be a major disruptive force in the healthcare industry before the end of the decade. According to a Gartner study published late last year, 10 percent of people in the developed world will be living with 3D-printed items on or in their bodies by 2019, and 3D printing will be a central tool in roughly one-third of surgical procedures involving prosthetic and implanted devices.
“A good example of that is prosthetics—it’s showing that technology can actually advance and help improve people’s lives,” said Kent Firestone, COO of Stratasys Direct Manufacturing.
Huber’s company, Standard Cyborg, sits right at the intersection of traditional medicine and new technology. Typically, prosthetic limbs are produced by taking measurements of the remaining limb and producing a copy in plaster, which is then modified to exact specifications using hand tools.
Standard Cyborg sells prosthetists 3D scanners and accompanying software that allows them to produce prosthetics in software, tinkering with the exact shape, and then printing them out. The end result is a functional prosthetic that was made in a fraction of the four hours it takes to build prosthetics the old-fashioned way.
Initially, practitioners viewed this technology as a threat. Now, most of the prosthetists Huber has either sold Standard Cyborg software to or talks to within the industry are more interested in bringing 3D printing and design into their medical practices, he said. The main reason is that 3D printing allows specialists to create complex geometrical shapes to ensure precise fits.
“Machines don’t care about complexity, and that’s going to be a huge deal for patient comfort,” he said.
Machines can also enable surgeons to create life-saving replicas of the human anatomy. Such was the case when researchers at the University of Michigan worked with surgeons at C.S. Mott Children’s Hospital in Ann Arbor to create and implant 3D-printed tracheal splints produced from biocompatible materials into five children who suffered from the congenital breathing condition tracheobronchomalacia. Designers are applying for an FDA investigational device exemption to treat 10 more patients.
But 3D printing technology still has some fundamental challenges to overcome. One big test in 2017 will be whether a simpler digital workflow can be made for creating and printing 3D objects, according to Dr. Jenny Chen, a neuroradiologist and the CEO of 3DHeals, a two-year-old company that organizes conferences and connects specialists in healthcare 3D printing.
“You want people to be able to interact with the technology, and you want that process to be streamlined,” she said. “If the barrier of entry is so high that people can’t input their creativity, it’s not going to accelerate innovation.”
In other words, the process of creating 3D objects in software and successfully printing them out is not push-button. It takes some skill and effort to create, for example, a 3D model of a brain. But if simplified software can make it easier for physicians and surgeons to interact with digital models, then 3D printing will more rapidly find its way into hospitals, university medical systems, and even private practices.
Then there are issues about whether 3D printed products can be manufactured at scale, although improvements are being made there.
The thorny regulatory issue is also an obstacle to widespread adoption. As of last year, the FDA had approved 85 3D-printed medical devices. Last May, the agency released draft guidance for manufacturers interested in produced 3D-printed medical devices.
Challenges notwithstanding, the potential promise of 3D printing technology is huge. Stratasys Direct Manufacturing’s Firestone said that more end-use parts, like surgical tools and device implants, will become more common in 2017 as sophisticated metal materials for 3D printing are refined and gain approval for human contact.
One such surgical tool built by Stratasys Direct Manufacturing is the Pathfinder, which assists surgeons in ACL reconstruction. The Pathfinder is registered as a Class I medical device with the FDA, and is now used by orthopedic surgeons across the U.S.
“As 3D printing has become more well known and talked about,” Firestone said, “we’re starting to see more applications that frankly we wouldn’t have thought of doing 10 years ago.”
Photo: Stratasys Direct Manufacturing