Some of the leanest, most efficient operating rooms and emergency rooms in North Carolina hospitals have the automotive industry to thank for their smoother running operations.
A growing number of healthcare facilities are incorporating so-called lean manufacturing techniques adapted from Toyota (NYSE:TM). Leannovation, an Apex, North Carolina company, is one company bringing such techniques to hospitals. Auto industry veteran Sean Lewis founded Leannovation in 2004, initially targeting other manufacturers before branching into other markets.
Lewis says the techniques of efficiency and continuous improvement can be applied anywhere there are systems in place. In that context, healthcare seems like a no-brainer as a target market. But Lewis’ decision to bring lean manufacturing tools to hospitals was more of a personal decision than a business one.
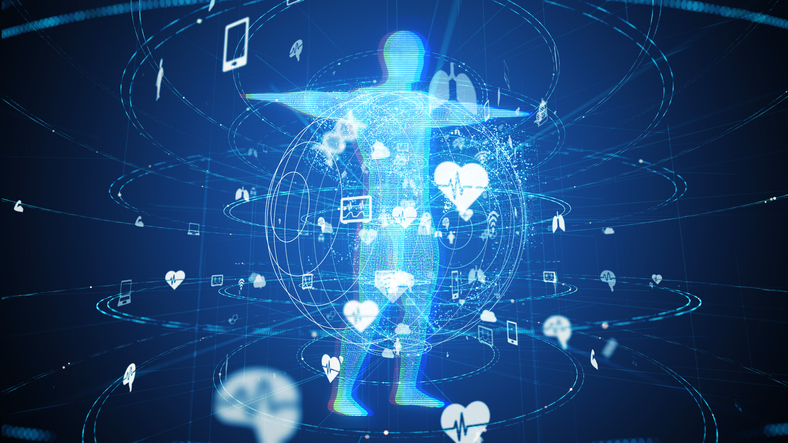
With the Rise of AI, What IP Disputes in Healthcare Are Likely to Emerge?
Munck Wilson Mandala Partner Greg Howison shared his perspective on some of the legal ramifications around AI, IP, connected devices and the data they generate, in response to emailed questions.
Several years ago, Lewis’ grandfather was hospitalized for what Lewis says was an unnecessarily long time. Lewis’ grandfather was administered the blood thinner coumadin. But the times he was given his dosage of the drug and the times when his blood levels were checked were mismatched, leading to an inability to manage the coumadin levels properly. The clinicians administering the drug weren’t communicating with those measuring the blood.
“This system needs lean badly,” Lewis recalls saying. “That’s why I got into health care.”
The Toyota Production System, often shortened to TPS, is a system developed by Toyota to boost the efficiency of its operations and eliminate waste. For example, components in the car manufacturing process are not ordered until they are needed, reducing the need to keep items in inventory. In modern manufacturing parlance, this concept is called “just-in-time.”
But the concept came from TPS where it’s called “kanban,” which translates as signboard or billboard. That means workers rely on signs to indicate what to do or how much of a product to order. In fact, many of the lean concepts retain their Japanese names when adapted for health care, as is evident in this video showing how a hospital kanban system works.
Until founding Leannovation , Lewis had spent his entire career in manufacturing, primarily automobiles. He worked first for Ford (NYSE:F), then Chrysler. Each company has a different name for its lean initiative; at Ford, it was the not very original “Ford Production System.” But the TPS system originated by Toyota is now widespread throughout the automotive and manufacturing industries in some form.
Lean’s benefits are now coming to healthcare. Terry Krauss, business development representative for Leannovation, says that the benefits come from studying the existing process and finding a way to make it better. Leannovation doesn’t have permission to disclose specific clients but as an example, Krauss cited a regional medical center in southern North Carolina whose OR supply management process was redesigned, saving more than $80,000 per year in expired inventory. When lean techniques were applied to OR scheduling, the hospital was able to take on six more surgeries per week with the same staffing levels working the same hours as before. More surgeries translates into more hospital revenue, he says.
While healthcare has systems that can readily adapt lean techniques, hospitals do present different challenges compared to manufacturing, Lewis said. When a manufacturing process is improved, the benefit can be immediately seen with results such as faster throughput. Those results aren’t always readily visible in health care. Part of that stems from the multiple silos that exist within health care, each with its own territory and power.
Territoriality is evident even within a single hospital where the ER, the OR and the ICU clash over various issues. Compounding the problem is fact that people in one silo often don’t see the processes that need improvement in the other silos. Bringing lean to hospitals, Lewis says, is not about making radical changes. It’s about changing processes over time, training employees and ultimately, getting the silos to communicate better.
Leannovation isn’t the only company pitching lean techniques, and it’s not even the only company pitching these techniques to hospitals. But while lean has a firm foothold in manufacturing, health care is still a relatively untapped market. That means there should be many opportunities for Leannovation and others. Lewis is betting on it. In the same way that lean became integral to automobile manufacturing, Lewis says lean will become just as important to health care.
“It’s going to be system that health care is going to be built around in the future,” he said.
[Photo courtesy of Flickr user Hugo90]