About 6 million people break their bones each year, according to the American Academy of Orthopedic Surgeons. But after fracturing his arm, one industrial design graduate used a 3-D printer to produce an exoskeletal brace. The result is an innovative concept for fixing broken bones that, if nothing else, has presented an interesting case for rethinking the traditional cast.
Victoria University graduate Jake Evill created the brace prototype with a homemade 3-D printer and nylon plastic.
In an interview with Wired magazine, Evill said the inspiration for his Cortex design came from the trabecular, a structure that forms the inner tissue of a bone.
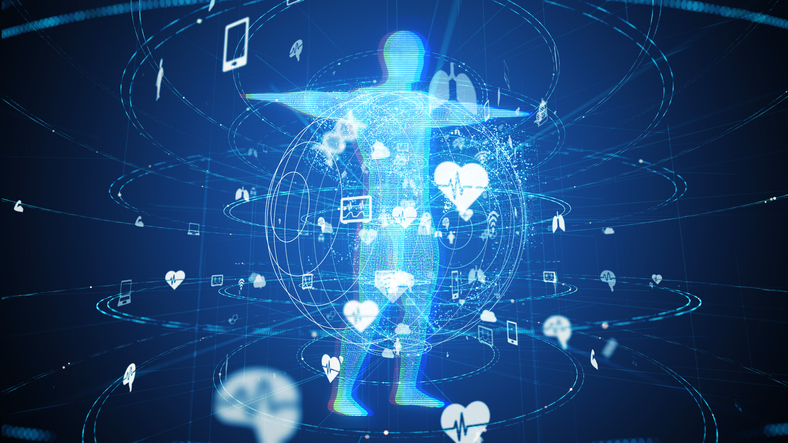
With the Rise of AI, What IP Disputes in Healthcare Are Likely to Emerge?
Munck Wilson Mandala Partner Greg Howison shared his perspective on some of the legal ramifications around AI, IP, connected devices and the data they generate, in response to emailed questions.
“It was this honeycomb structure that inspired the Cortex pattern because, as usual, nature has the best answers,” he said. “This natural shape embodied the qualities of being strong whilst light just like the bone it is protecting within.”
Patients being fitted for these braces would have an X-ray taken and then a scan of the injured arm or leg. A computer would assess the optimal pattern and structure for the cast.The honeycomb design would do away with the stinky, sweaty yuckiness that accompanies plaster and fiberglass casts and allow more breathing room for the skin.
Evill has emphasized that the Cortex cast is still a work in progress. For one thing, the 3-D generated version takes much longer to produce than a plaster cast, which only takes a few minutes. But Evill, who developed the design in collaboration with Victoria University’s orthopedics department, is looking for collaborative partners and a hospital to pilot it.
Finding new ways to accelerate the healing process for fractures has been a big priority in orthopedic medicine. Stem cell therapy has garnered a lot of attention. But some other approaches include using polymers to create a form of scaffolding and converting pre-evaluated blood plasma into a biologically active putty to accelerate healing for sports-related bone injuries.
Of course it’s not the first orthopedic concept produced with a 3D printer. The U.S. Food and Drug Administration cleared a skull implant developed by Oxford Performance Materials called OsteoFab Patient Specific Cranial Device.