Big medtech companies have been criticized for their diminishing innovation record, especially from this blog. One of the few innovation strengths that large companies should exhibit is manufacturing. And, I’m not referring to advanced manufacturing in itself, but the synergy between manufacturing and R&D.
In the mid-nineties, I had the pleasure to experience Cordis Corporation (pre- J&J buyout) co-locate its product development infrastructure with its manufacturing operations. Having come from a company that had no such interaction, I was enamored with the effect.
Every conceptualized new product and technology has to be fabricated. A medical device company that has expertise in orthopedics, catheters, or pacemakers, contains specialized manufacturing equipment, tools, resources, etc. that applies to their specific field. This manufacturing proficiency can fuel innovation.
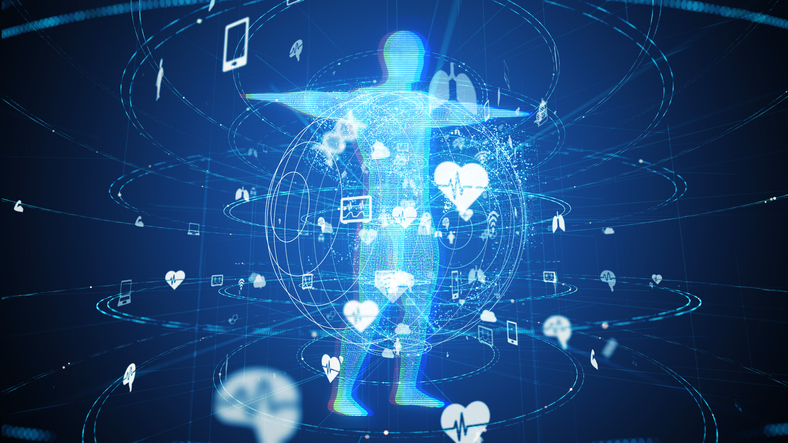
With the Rise of AI, What IP Disputes in Healthcare Are Likely to Emerge?
Munck Wilson Mandala Partner Greg Howison shared his perspective on some of the legal ramifications around AI, IP, connected devices and the data they generate, in response to emailed questions.
The ability to instantly pull a few technicians and equipment off the production floor and create a pilot manufacturing operation on a novel product provides huge advantages. Despite the nimbleness of a start-up company, the effort involved with creating the same pilot operation is incomparable.
A recent article by Annie Lowrey in the New York Times, “High-Tech Factories Built to Be Engines of Innovation”, made me reminisce about those Cordis days and how large medtech companies have tossed this tremendous manufacturing advantage to the wayside in the nearsighted pursuit of lower COGS (cost of goods sold).
In the case of Cordis, most domestic manufacturing was transferred to Juarez, Mexico. A huge strength was immediately turned into a liability. No longer could we rapidly pilot manufacture a new product for clinical trials and product introductions instantaneously slowed down.
Ms. Lowrey quotes Mitzi Montoya, dean of the college of technology and innovation at Arizona State University, “In sector after sector, we’ve lost our innovation edge because we don’t produce goods here anymore.”
On paper, the bean-counters might show greater profit created by the exporting of manufacturing to low cost and low skill locations. But, what the spreadsheets don’t describe is the cost in time and execution of new product introductions, clinical trial initiations, etc. and increase in product recalls and inferior product performance.
More impactful to innovation, the fracturing of the collaboration between manufacturing and R&D makes large companies less likely to embark on novel product development. If a company is going to throw a product “over the fence” to a Mexican manufacturing facility, why not let a start-up company develop the product and transfer production to an outsourced manufacturing facility.
The exporting of medical device manufacturing has paralleled the trend towards start-up companies increasingly being relied on for new medical device innovation.
Large companies have their limitations, which we have highlighted in the past, but not leveraging a company’s strengths is wasteful and eventually the core competencies that have made leading medtech companies successful are gone and leave behind a shell of marketing and sales.
Healing Innovation is a resource for clinician innovators. The main site - HealingInnovation.com - provides an overview of the various aspects and issues facing clinician innovators.